Evaluation of Dispersion and Throughput in Calcium Carbonate-Filled Compounds
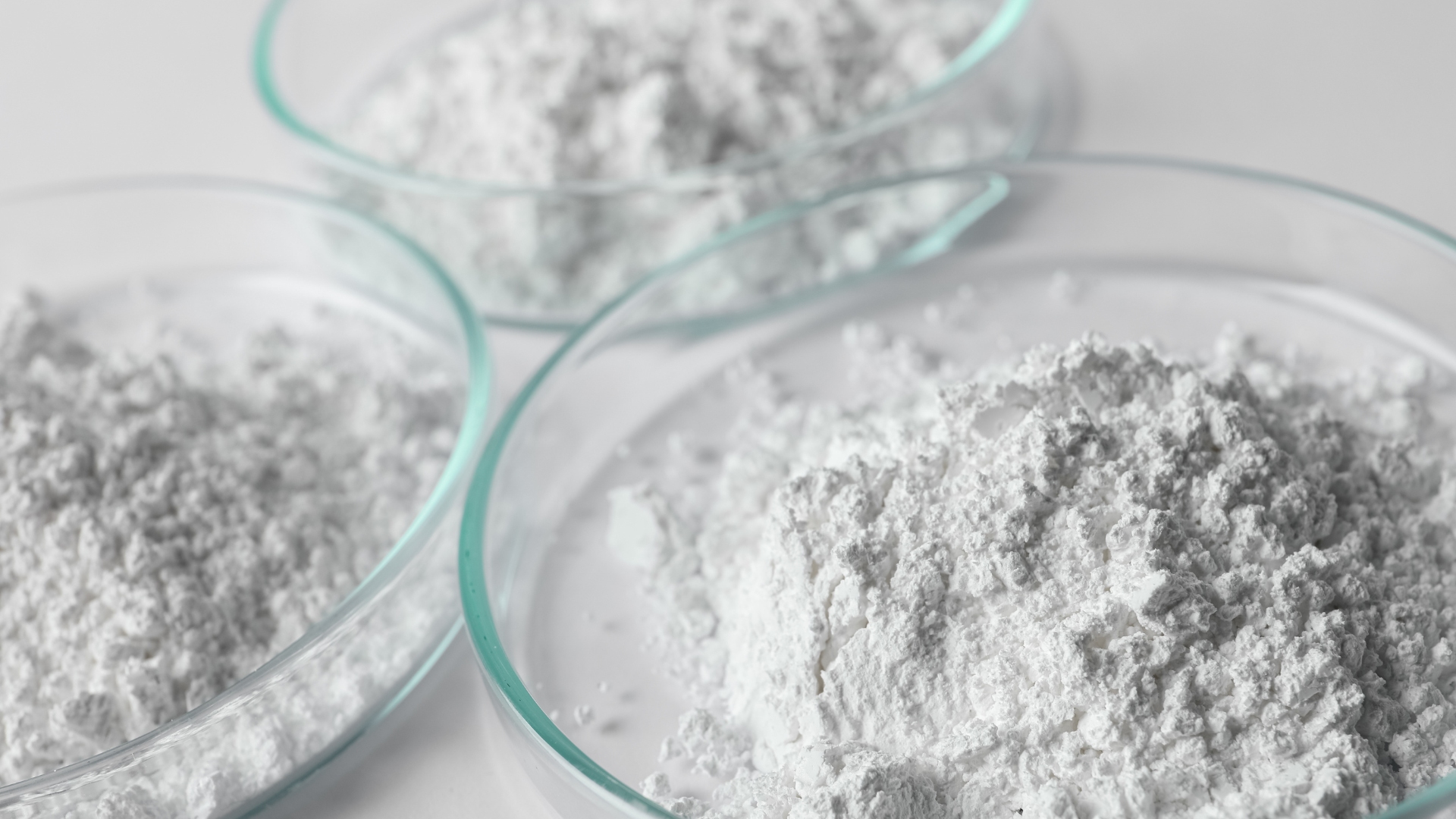
At CTE, we continuously conduct performance testing to establish stable, high-throughput extrusion conditions for high-filler compounds. In this test, we evaluated the dispersion and throughput of a compound containing over 60% calcium carbonate (average particle size 1.2 μm) blended with LLDPE.
High-filler formulations present common challenges such as poor dispersion and difficulties in maintaining high output rates. To address these, we compared the performance of our HTM Tandem Compounding Twin-Screw Extruder against a conventional co-rotating intermeshing twin-screw extruder.
Test Results
HTM Tandem Compounding Twin-Screw Extruder
Dispersion Performance
We measured Filter Pressure Value (FPV) to evaluate dispersion. The compound processed with the HTM-38 Tandem Extruder at 80% calcium carbonate concentration showed equivalent FPV to the compound produced by a conventional extruder at 60%, indicating superior dispersion capability at higher filler loadings.
Throughput Performance
The conventional 65 mm twin-screw extruder achieved 350 kg/h at 60% calcium carbonate concentration. In contrast, the HTM-38 Tandem Extruder (38 mm screw diameter) achieved 140 kg/h, equivalent to 530 kg/h when scaled to 65 mm. The HTM-38 also successfully processed 70% and 80% filler content at 100 kg/h (equivalent to 380 kg/h at 65 mm).
Balancing Throughput and Dispersion
The test demonstrated that the HTM Tandem Extruder maintained comparable dispersion to the conventional machine at 60% filler while delivering approximately 1.5 times the throughput. It also enabled higher filler content processing, maintaining stable output even at 70% and 80% calcium carbonate concentration—something difficult with conventional systems.
CTE’s Extrusion Solutions
Based on this evaluation, the strengths of CTE’s HTM Twin-Screw and HTM-38 Tandem Extruders can be summarized as follows:
1. Efficient high-filler compounding with stable, high-throughput performance
2. Rotor design enables excellent kneading while minimizing shear heat
3. Independent single-screw discharge section allows for lower resin temperature extrusion
CTE continues to develop advanced extrusion conditions through testing and technical support. We offer extrusion trials and material analysis for a wide range of applications, including high-filler compounds, recycled materials, and biodegradable resins. Please contact us to discuss optimized extrusion solutions tailored to your materials.