Advanced Plastic Extrusion Solutions for Low Bulk Density Materials
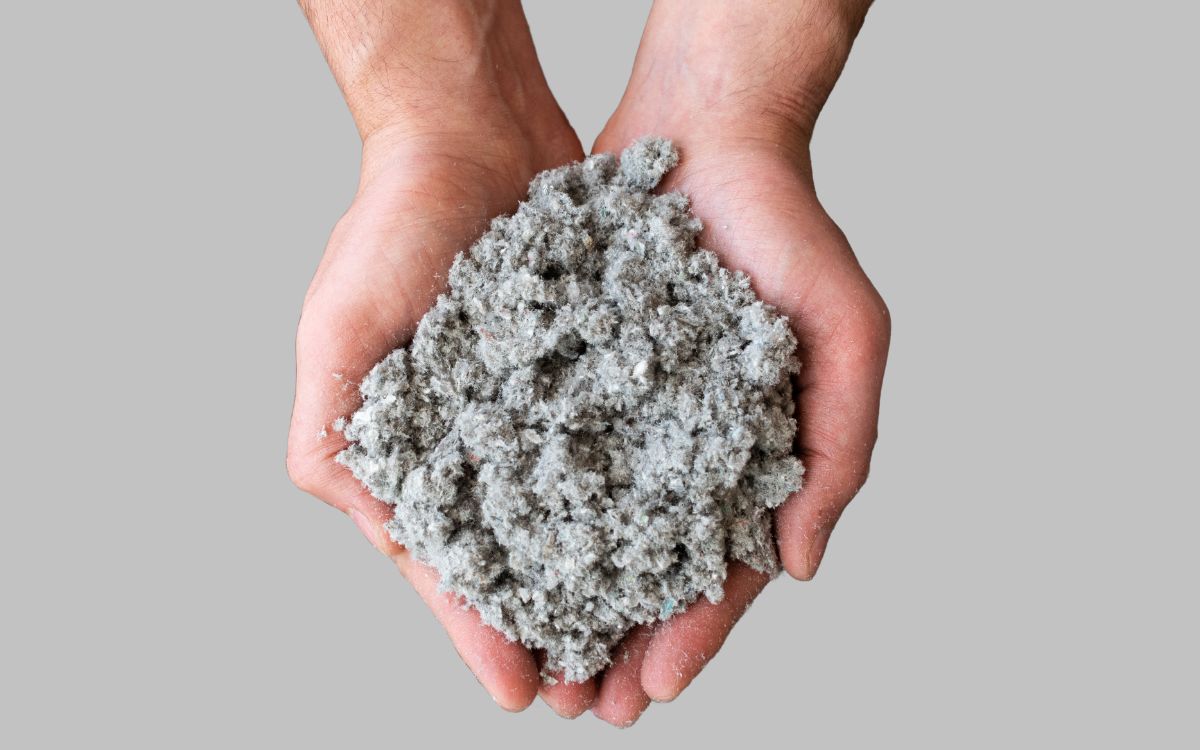
As the demands on plastic compounding technology grow increasingly sophisticated, the industry faces new challenges. With the rise of cutting-edge materials such as fine fillers and cellulose nanofibers (CNF), manufacturers must address diverse needs, including sustainability and recycling. However, these advanced materials often have low bulk density, making them difficult to feed into conventional co-rotating twin-screw extruders. This can result in unstable throughput and compromised product quality.
CTE’s HTM Twin-Screw Kneading Extruder is specifically designed to overcome these challenges. With a unique non-intermeshing, counter-rotating screw system and superior degassing capabilities, it ensures smooth material feeding and efficient processing, even with low bulk density materials.
In this article, we’ll explore how CTE’s innovative solution addresses the unique challenges of processing low bulk density materials, backed by real-world success stories.
Challenges with Low Bulk Density Materials
“What is Bulk Density?”
Bulk density refers to the mass of material per unit volume and indicates how tightly a material is packed. Low bulk density materials, such as fine fillers, cellulose nanofibers (CNF), cellulose microfibers (CMF), glass flakes, and wood flour, are characterized by their high air content.
These materials often cause feed necking during feeding, disrupting the extrusion process and reducing stability. Traditional co-rotating twin-screw extruders struggle with these materials, leading to inadequate degassing and increased quality risks for the final product.
Why Do These Issues Occur?
Low bulk density materials inherently trap more air. During extrusion, trapped gases can accumulate, causing feed blockages and significant reductions in processing efficiency. This makes stable and high-quality production challenging without advanced equipment.
CTE’s HTM Twin-Screw Kneading Extruder: A Game-Changing Solution
CTE’s HTM Twin-Screw Kneading Extruder offers a cutting-edge design tailored to low bulk density materials. Its key features include:
Non-Intermeshing Screw Design:
The non-intermeshing screw configuration minimizes material retention, preventing feed necking and ensuring consistent throughput.
Superior Degassing Performance:
The HTM extruder incorporates a rear vent system, allowing trapped gases to escape efficiently through gaps between the screws. This eliminates gas accumulation and stabilizes the extrusion process.
Efficient Processing for Low Bulk Density Materials:
The advanced screw design ensures that even air-heavy materials are fed smoothly, enabling high throughput and stable production.
Real-World Success Stories
CTE’s HTM Twin-Screw Kneading Extruder has been successfully adopted across industries that process low bulk density materials, demonstrating exceptional performance in achieving stable production and high-quality outputs.
Conclusion
Processing low bulk density materials comes with unique challenges, but CTE’s HTM Twin-Screw Kneading Extruder provides an effective solution. By addressing feed necking and degassing issues, this innovative technology ensures stable, efficient production. Whether you’re working with high-filled compounds or tackling recycling challenges, the HTM extruder delivers reliable, high-performance results.