HTM Tandem Compounding Twin Screw Extruder
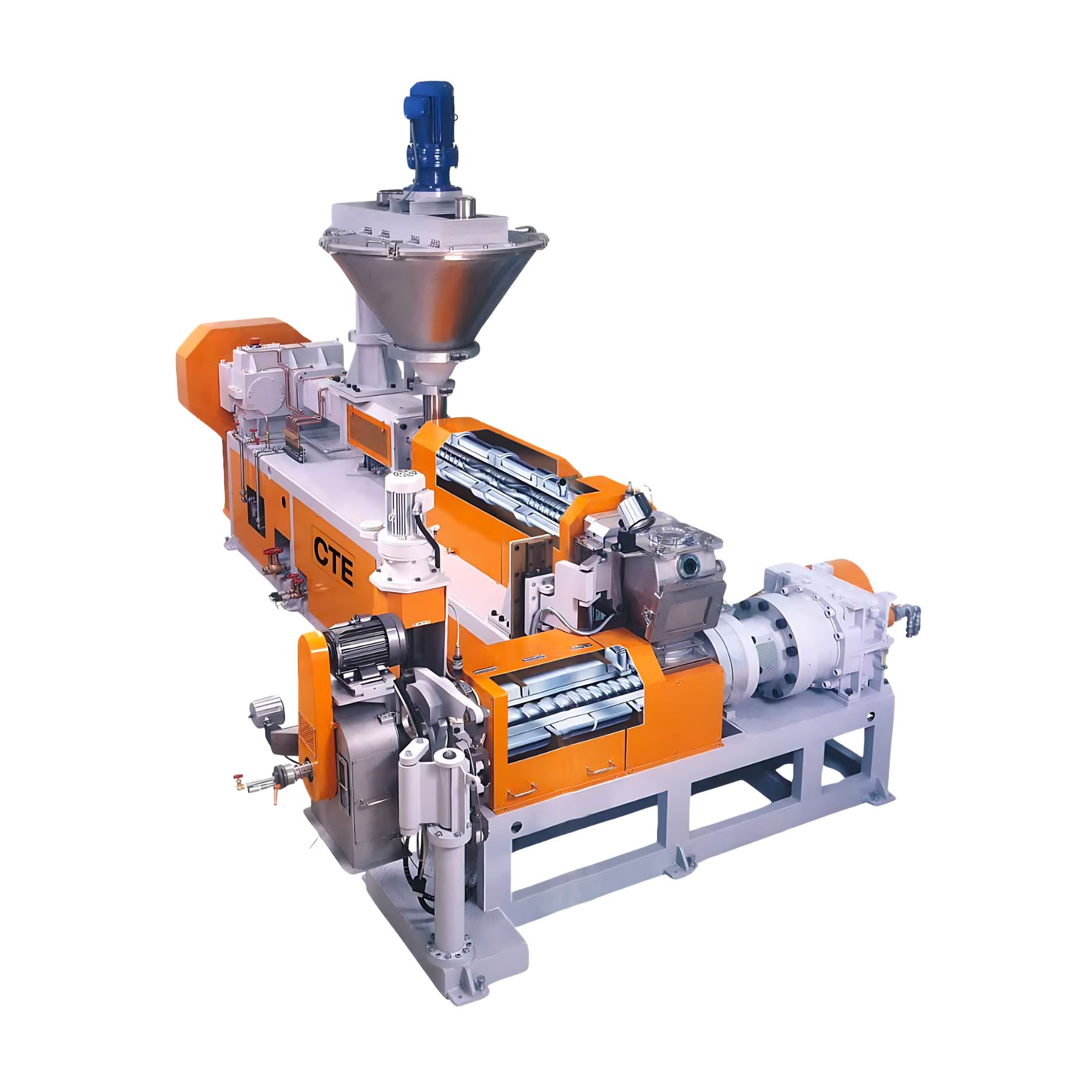
- #Talc
- #HighFillerCompounding
- #ContainerRecycling
- #ChemicalRecycling
- #MaterialRecycling
- #Recycling
- #PBAT
- #BiodegradableResin
- #RecycledPVC
- #PVC
- #BiomassMaterial
- #CalciumCarbonate
- #TitaniumDioxide
- #InorganicFiller
- #RigidPVC
- #FineTalc
The Ultimate Solution for High-Filler Compounding and Superior Recycled Pellet!
Upgraded HTM Twin-Screw Extruder Model!
The HTM Tandem Compounding Twin-Screw Extruder builds upon the renowned HTM Twin-Screw Extruder technology, delivering world-class performance in high-filler compounding and recycled pellet production. This advanced system, with its counter-rotating, non-intermeshing twin-screw section combined with a large-diameter single-screw section, allows for precise control and exceptional efficiency in compounding operations.
- Features
- Applications
- Formulation Guide
- Specifications
- Product Catalog
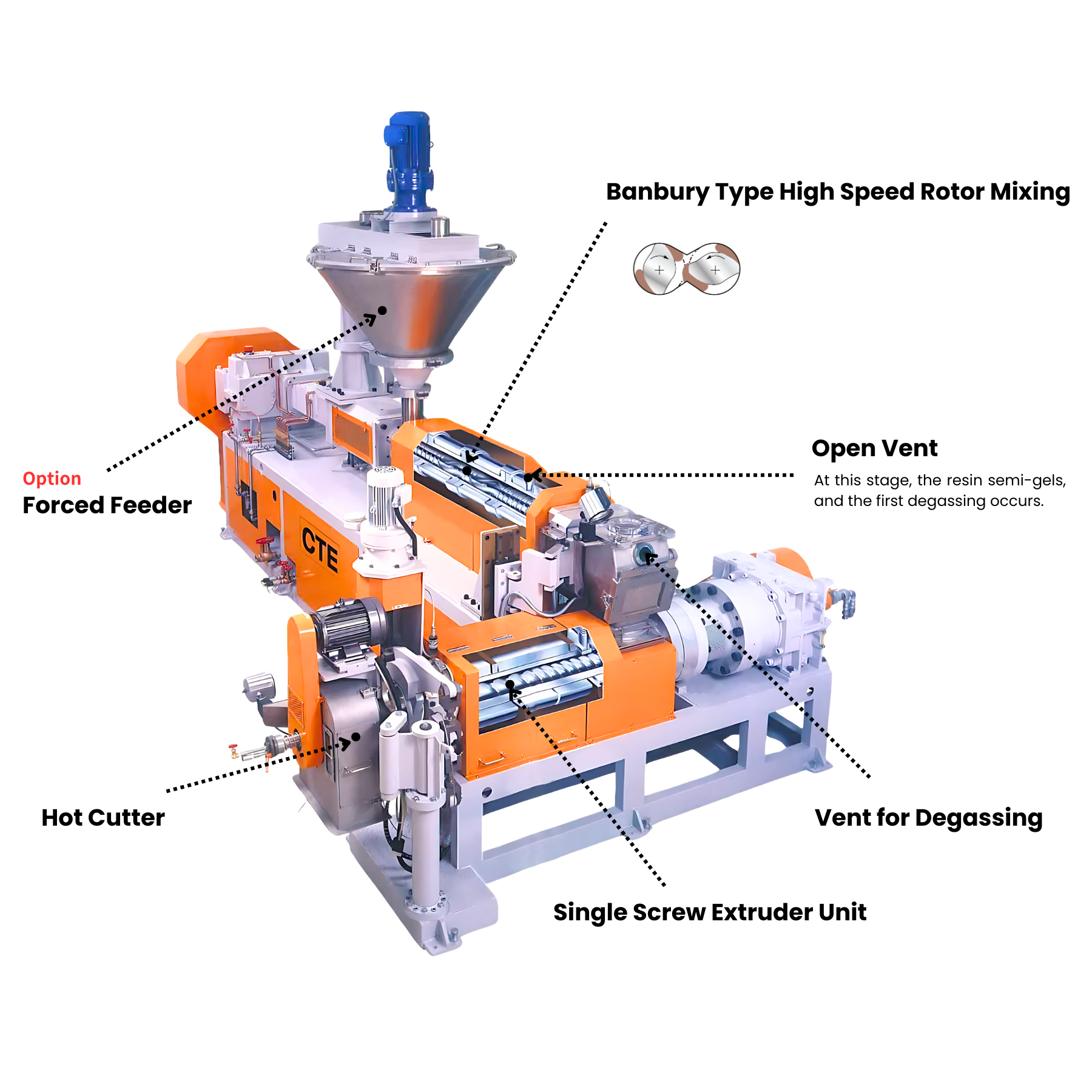
1. Superior Kneading Performance
The HTM Tandem Compounding Twin-Screw Extruder utilizes multiple high-speed rotors, similar to those in Banbury mixers, providing superior kneading performance. This system achieves significantly higher kneading efficiency compared to co-rotating twin-screw extruders, making it ideal for high-filler compounding. After kneading and vacuum degassing, materials are extruded at low speed through a large-diameter single-screw, enabling lower-temperature extrusion than the HTM Twin-Screw Extruder. This results in high-quality output for compounding applications.
2. Segmented Screw Design for Flexible Compounding
The system’s segmented screw design, similar to the HTM Twin-Screw Extruder, allows for flexible adjustments to rotor type and number, enabling the processing of various resins. This feature supports a wide range of compounding applications, including the production of recycled pellets, while ensuring consistent high-quality mixing.
3. Low-Temperature, Low-Speed Extrusion for High-Filler Compounds
In the downstream large-diameter single-screw section, the system operates at lower temperatures and speeds than previous HTM models. This reduces material degradation and burning, making the extruder especially effective for high-filler compounding and the extrusion of rigid PVC.
4. Superior Kneading Comparison by Rotor Design
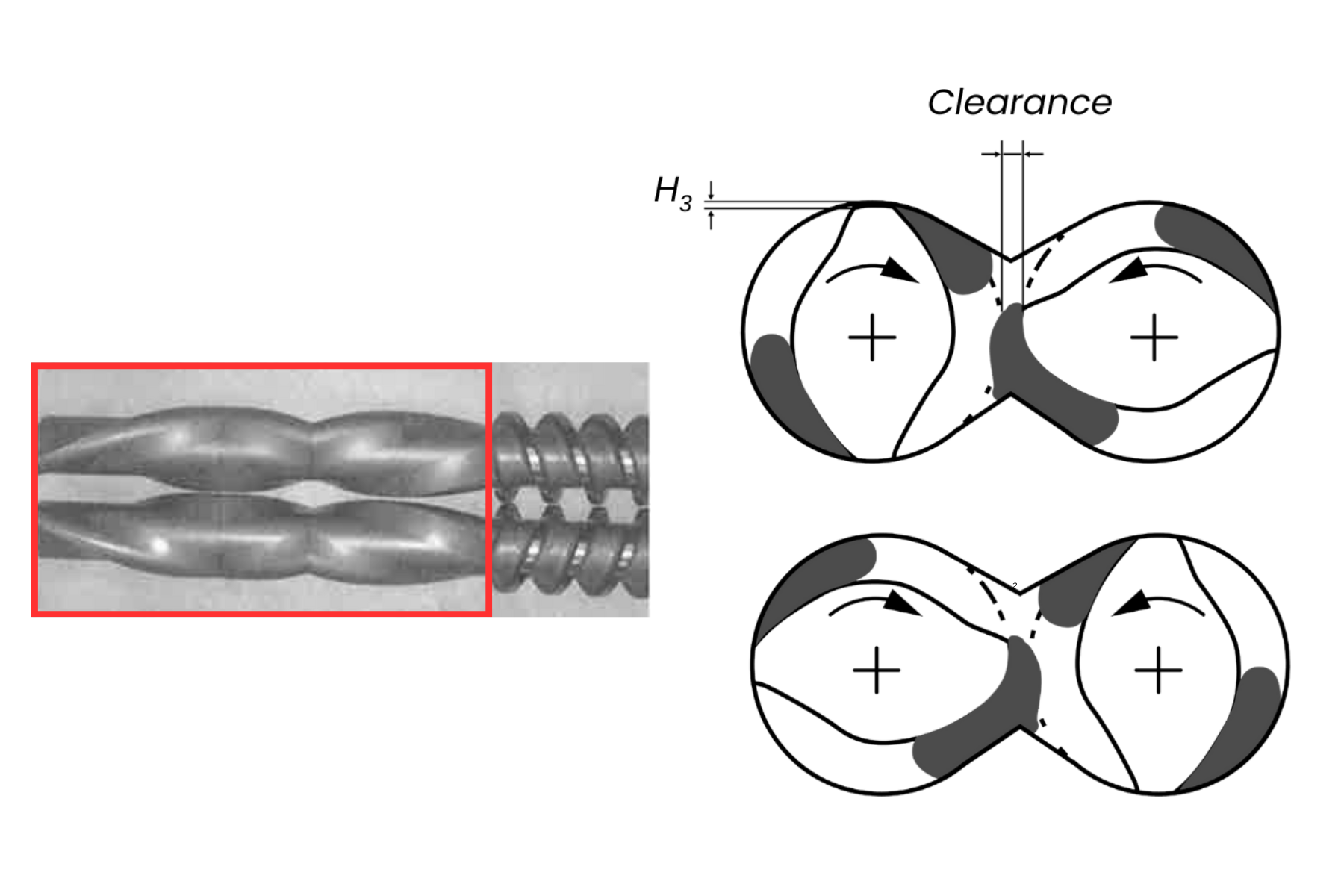
HTM Technology (Kneading Rotor):
Resin passes through the rotor’s clearance, undergoing compression and release, providing high-shear, low-heat kneading. This ensures superior kneading efficiency, crucial for compounding and high-filler materials.
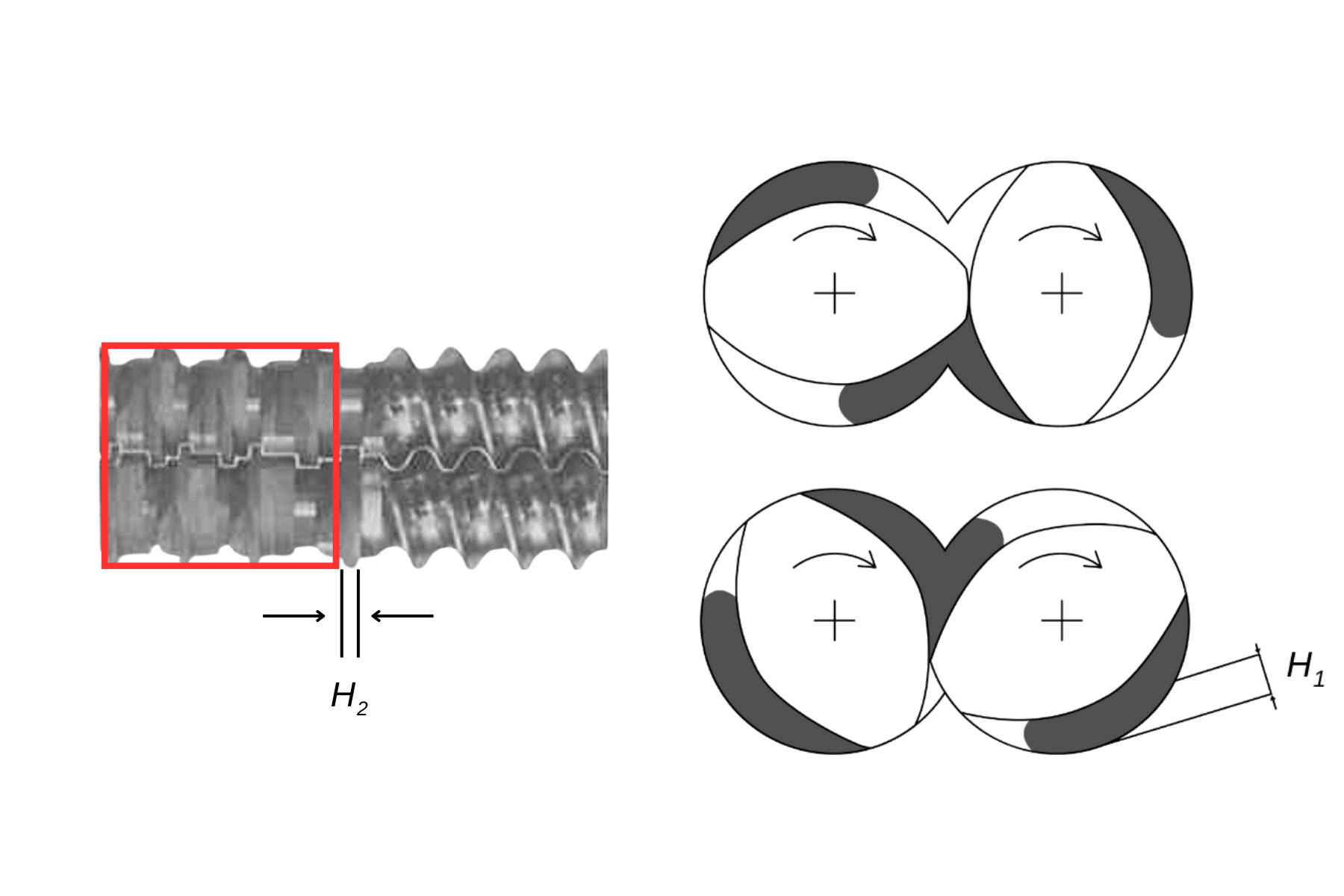
Conventional Technology (Kneading Disc)
Resin remains under continuous high compression with medium shear, which generates more heat and less effective kneading, making it less suitable for high-filler compounding.
5. Resin and Gas Movement
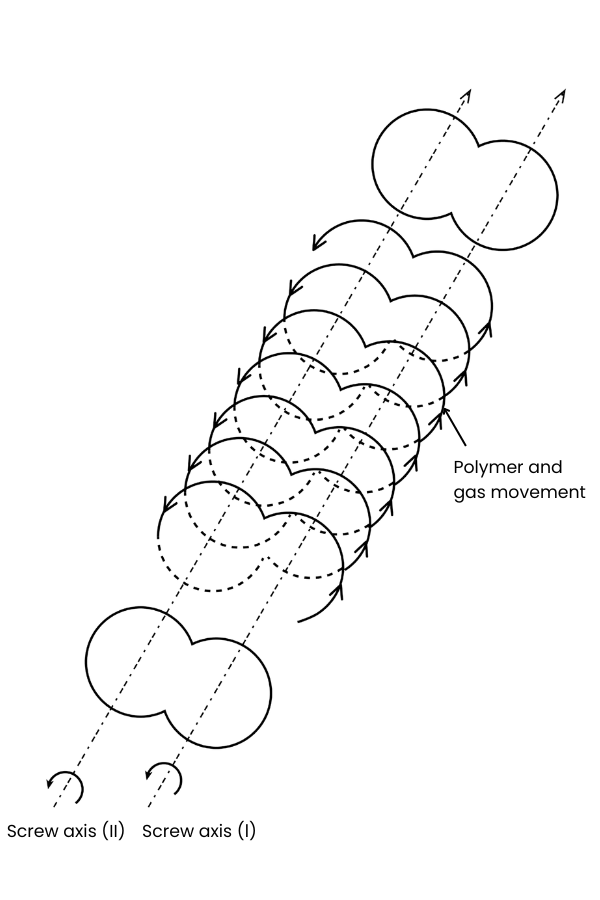
HTM Twin-Screw Extruder
(Non-intermeshing, Counter-Rotating)
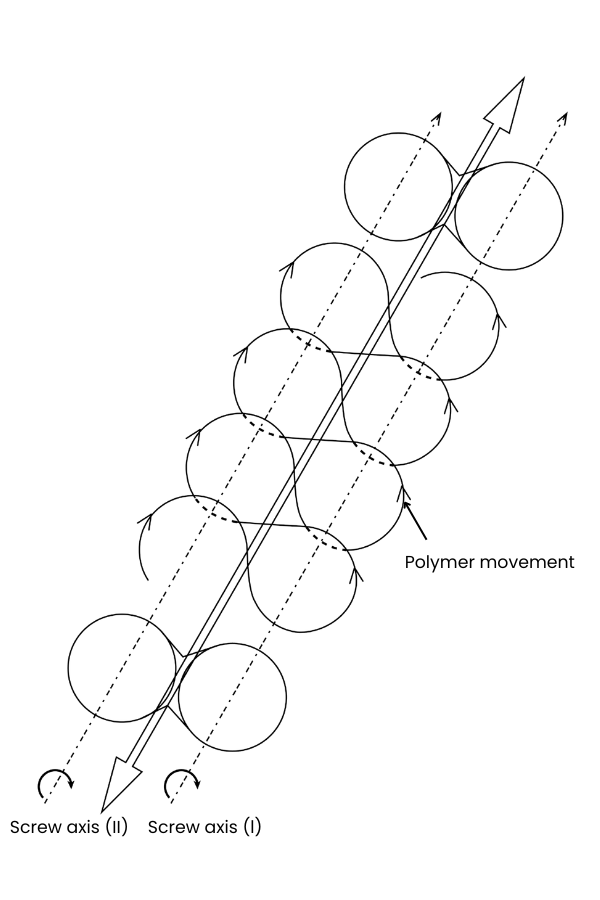
Conventional Twin-Screw Extruder
(Intermeshing, Co-Rotating)
6. Exceptional Degassing Performance
The counter-rotating, non-intermeshing design of the HTM Tandem Compounding Twin-Screw Extruder offers significantly better degassing performance. This helps prevent air bubbles in recycled pellets, reducing molding defects and improving product quality. By efficiently venting expanding air, the system eliminates feed neck problems, which are common in conventional twin-screw extruders.
Technology | CTE’s Patented Technology (Counter-Rotating, Non-Intermeshing Type) |
Conventional Technology (Co-Rotating, Intermeshing Type) |
---|---|---|
Gas Venting Design | The two screws do not intermesh, with a gap between them. Gas and air escape through the gap, resulting in excellent gas venting. | The two screws intermesh, causing gas to move only along the grooves, resulting in poor gas venting. |
Kneading | The resin undergoes high shear by the rotors and is evenly kneaded. The repeated compression and release allow for high kneading efficiency and low-temperature extrusion with reduced heat generation. | The resin is continuously sheared under high compression, leading to significant heat generation even with minimal kneading. |
Low-Temperature Extrusion | After melting and kneading in the HTM twin-screw section, the single-screw extrusion section minimizes heat generation. | The extrusion section after kneading is twin-screw, making it prone to heat generation. |
Dispersibility | ◎ Excellent | 〇 Good |
Shear Heat Suppression | ◎ Excellent | △ Needs Improvement |
Gas Venting | ◎ Excellent | △ Needs Improvement |
Material Feeding | ◎ Excellent | △ Needs Improvement |
Productivity | ◎ Excellent | 〇 Good |
Maintenance | 〇 Good | 〇 Good |
Resin Temperature Control | ◎ Excellent | △ Very Inferior |
Material Applicability | ◎ Excellent | △ Needs Improvement |
High-Performance Solution for Chemical & Material Recycling and Biodegradable Resin Processing!
Highly regarded in the fields of chemical recycling and material recycling, the HTM Tandem Compounding Twin-Screw Extruder offers industry-leading degassing and kneading capabilities. This helps prevent bubble formation in pellets and significantly enhances material properties, making it a go-to solution for efficient recycling processes and the production of high-quality recycled pellets.
The system excels in reprocessing ocean waste plastics (such as fishing nets) and plastic components from used home appliances, cables, PET bottles, and food trays. It also provides superior performance in compounding biomass and biodegradable resins, positioning it as an ideal choice for eco-conscious industries.
Formulation Guide
Compound and Extrusion Rate Examples (kg/h)
The extrusion rates in the table are reference values.
Example: HTM-38/75 → Twin-screw diameter = 38mm, Single-screw diameter = 75mm
Formulation Guide | Model | ||||||
---|---|---|---|---|---|---|---|
HTM-38/75 | HTM-50/100 | HTM-65/130 | HTM-78/150 | HTM-90/180 | HTM-105/210 | HTM-120/240 | |
Rigid Material (PP) | 130 | 250 | 500 | 750 | 1000 | 1500 | 2000 |
PP (MFR 30) + Fine Talc 85% | 100 | 200 | 400 | 600 | 800 | 1200 | 1600 |
HDPE (MFR 0.5) + Standard Talc 60~80% | 100 | 200 | 400 | 600 | 800 | 1200 | 1600 |
LLDPE + Shell-Derived Calcium Carbonate 60% | 100 | 200 | 400 | 600 | 800 | 1200 | 1600 |
PBAT + Calcium Carbonate 70% | 75 | 150 | 300 | 450 | 600 | 900 | 1200 |
PLA + Calcium Carbonate 70% | 75 | 150 | 300 | 450 | 600 | 900 | 1200 |
Rigid PVC | 75 | 150 | 300 | 450 | 600 | 900 | 1200 |
Rigid PVC + CMF/CNF 30% | 50 | 100 | 200 | 300 | 400 | 600 | 800 |
RPVC + Shell-Derived Calcium Carbonate 30% | 75 | 150 | 300 | 450 | 600 | 900 | 1200 |
LDPE + CMF 30% | 75 | 150 | 300 | 450 | 600 | 900 | 1200 |
LDPE + Titanium Dioxide 80% | 50 | 100 | 200 | 300 | 400 | 600 | 800 |
Other various material compounding results available. Please contact us for details.
Extruder | Specification | Model | ||||||
---|---|---|---|---|---|---|---|---|
HTM-38/75 | HTM-50/100 | HTM-65/130 | HTM-78/150 | HTM-90/180 | HTM-105/210 | HTM-120/240 | ||
HTM-Type Extruder (Twin-screw Section) | Screw Diameter / mm | 38 | 50 | 65 | 78 | 90 | 105 | 120 |
Max Screw Rotation Speed / rpm | 800 | 700 | 700 | 600 | 550 | 500 | 450 | |
Motor Capacity / kW | 37 | 75 | 160 | 250 | 350 | 500 | 650 | |
IPE-Type Extruder (Single-screw Section) | Screw Diameter / mm | 75 | 100 | 130 | 150 | 180 | 210 | 240 |
Max Screw Rotation Speed / rpm | 50 | 50 | 50 | 50 | 50 | 50 | 50 | |
Motor Capacity / kW | 15 | 30 | 45 | 75 | 110 | 185 | 250 |
※上記は標準仕様のため、御客様の要求仕様により変更致します。