Evaluation Test for High-Filler, High-Dispersion Compounding: HTM Tandem Twin-Screw Extruder
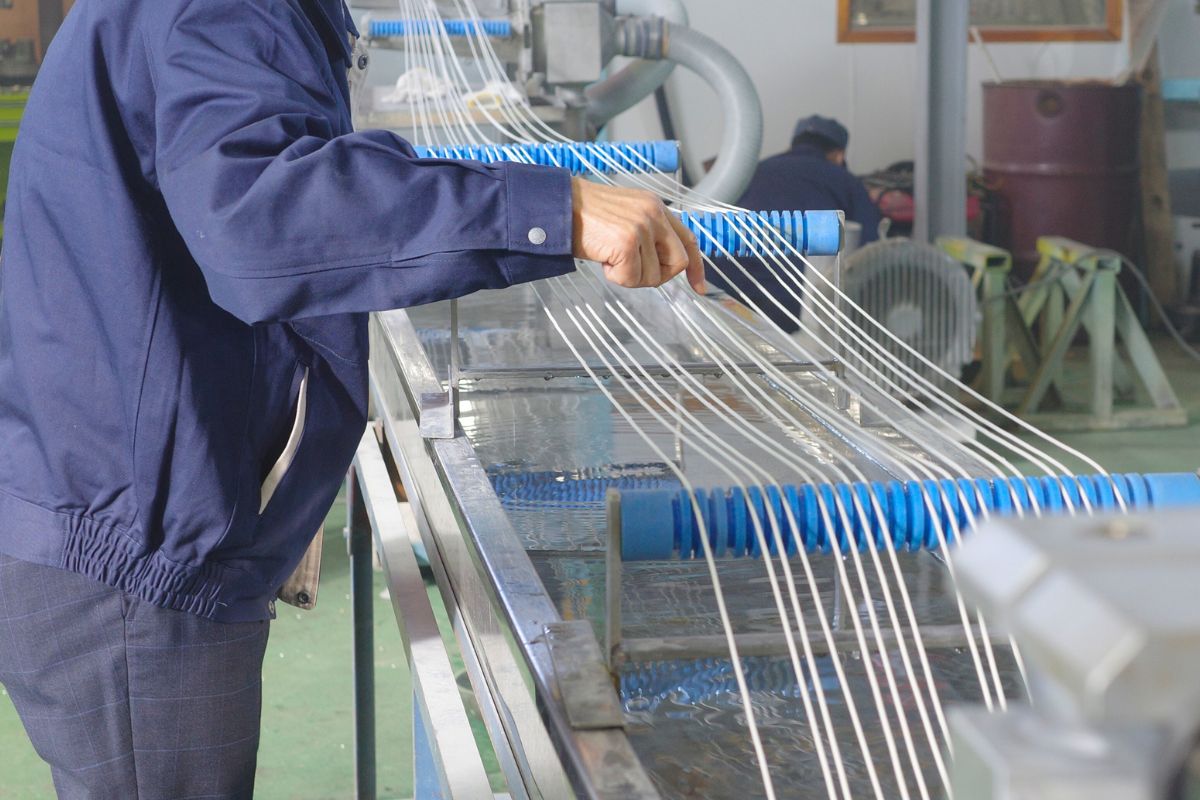
A CTE technician adjusting the extruded strands passing through the cooling water tank, highlighting the importance of quality control and cooling processes in the extrusion operation.
In general, as filler particle size decreases, achieving uniform dispersion becomes more challenging. Additionally, lower bulk density fillers tend to trap more air and moisture, leading to feeding inconsistencies such as feed necking. Consequently, achieving high filler loadings while maintaining product quality remains a key challenge in compounding.
CTE’s HTM-Series Twin-Screw Extruders are designed to address these challenges. In this test, we utilized the HTM-38 Tandem Twin-Screw Extruder to evaluate its performance in compounding calcium carbonate (average particle size 1μm) with polypropylene (PP).
Test Background and Objectives
Producing high-filler masterbatches with fine particle fillers presents three major challenges:
Dispersion Performance: Traditional systems struggle with calcium carbonate agglomeration, leading to surface defects (white specks).
Throughput Capacity: Increasing output often results in feed necking and insufficient dispersion.
High Filler Loading: Higher calcium carbonate concentrations exacerbate feed necking issues.
This evaluation aimed to verify whether the HTM-38 Tandem Twin-Screw Extruder could effectively address these challenges.
The test focused on the following key objectives:
1) Minimizing white speck formation caused by agglomeration.
2) Maintaining product quality at high output rates.
3) Ensuring process stability at high filler loadings.
Specifications of HTM-38 Tandem Twin-Screw Extruder and IPE-75 Single-Screw Extruder.
The comparison chart outlines the specifications of both extruders, including screw diameter, L/D ratio, motor power, maximum screw speed, and vent type.
The auxiliary equipment includes:
1) LIW Feeders: Twin-screw for powders, single-screw for pellets.
2) Hopper Screw: Not used.
3) Strand Cutting System: Featuring a Φ4.0×9-hole die.
Test Results
1. Dispersion Performance
The test results demonstrate the impact of different process conditions on material dispersion and surface quality.
The press sheet images show a significant difference: the left sample (1) exhibits poor dispersion, whereas the right sample (4) shows excellent dispersion.
By optimizing temperature and screw speed, dispersion performance improved, effectively reducing the occurrence of white specks.
2. Throughput Capacity
Samples processed at various output rates (30kg/h, 50kg/h, 75kg/h, 100kg/h) illustrate the changes in dispersion and material quality.
With a 30% calcium carbonate loading, the extruder achieved a maximum throughput of 75kg/h at 500 rpm.
When increasing the throughput to 100kg/h, white specks were observed at the same screw speed.
The results confirmed the balance between high output and dispersion quality, demonstrating enhanced production efficiency.
3. High Filler Loading Capability
Comparison of test samples with varying filler concentrations (30%, 60%, 70%) highlights the influence of loading levels on dispersion and surface quality.
Even with a 70% calcium carbonate loading, excellent dispersion was achieved.
The test confirmed the extruder’s capability to handle high-filler masterbatches with superior consistency.
Conclusion
The evaluation proved that the HTM-38 Tandem Twin-Screw Extruder offers a reliable solution for addressing the challenges of dispersion and processing capacity in high-filler compounding. Moreover, with an upgraded motor and enhanced screw speed, stable dispersion performance can be maintained even at 100kg/h or higher.
Furthermore, introducing a hopper screw feeder can eliminate bridging issues that commonly occur with high filler loadings (above 70%), ensuring stable material feeding and continuous operation.